1. OH & S Management
2. Physical Hazards
3. Chemical Hazards
4. Fire and Explosion Hazards
5. Industrial Hygiene / Occupational Health
This Audit review / verifies following documents :
- OH & S Policy;
- Safety Organization Chart;
- Training records on safety fire and first-aid;
- Record of plant safety inspections;
- Accident investigation reports;
- Accidents, dangerous occurrences and near miss incident – statistics and analysis;
- Record of tests and examinations of equipment and structures as per statues;
- Standard Operating Procedures (SOPs) for various operations;
- Record of Work permits;
- Record of work environment monitoring (flammable, toxic and explosive substances);
- Maintenance, testing and calibration records of fire detection and fire fighting equipment;
- Medical records of employees;
- Record of Industrial Hygiene surveys (Noise, Ventilation, Illumination, Dust etc.);
- Material Safety Data Sheet (MSDS);
- On-Site emergency plans and record of Mock Drills;
- Records of storage of hazardous solid waste and its disposal;
- Records of gaseous emissions and effluent discharge to the environment;
- Housekeeping inspection records;
- Minutes of safety committee meetings;
- Statutory licenses and approvals;
- Records of any modifications carried out in plant or process;
- Maintenance procedure and records;
- Instrumentation and equipment calibration and testing records;
- Planned shutdown maintenance procedures;
- In service inspection manuals, records including that of material handling;
- OH & S budget;
- Inspection books and other statutory records;
- Records of previous audits and safety analysis;
- Procedures for safe transportation of hazardous substances;
- Calibration records;
- Records for breakdown of plants during the process of manufacture;
- Records for waste material generated and their disposal;
- SOP for disposal of waste materials;
- Records for issue of PPE items to the personnel working in process building.
Safety Signage are being provided to enhance aesthetics,give important information,guidelines and message to employees,contractors and any type of visitors. All signage specifies standards for design,finishing,fixtures,color,size,letters and other items for all Buildings, Plant premises/ Operational areas , Offices etc.
Design of Safety Signage are based on their functionality,location and message to user.
Important considerations are :
1. Legibility
2. Signage Size
3. Illumination
4. Material
5. Language
6. Color schemes
7. Other USPs for expression
Chemicals are ubiquitous in commerce and industry, and warehousing of chemicals and chemical products is an essential part of those activities. While many of the practices and standards applied to safe warehousing of chemicals are similar to those followed for safe warehousing of a wide range of other materials and commodities, chemicals may present unique safety, environmental or property protection challenges.
To identify and address those issues unique to chemical warehousing while recognizing the large areas of commonality with other types of warehousing operations.
Safe warehousing of chemicals requires a multi-faceted approach that integrates a wide spectrum of issues and can be applied to new warehouses in the planning stage or existing one.
The identification of potential hazards associated with the warehouse storage of chemicals in various container and packaging systems/ mode of storage. The hazards that are addressed include health effects, environmental pollution, fire and explosion and their means to minimize risk to employees, the surrounding population, the environment, property and business operations.
Warehouses can be located on a manufacturing site or be free-standing facilities. It can be companies built in part or leased.
Heavy Equipment Movement is an activity involving Loading, Unloading, Storage and Movement from one place to another, lifting and erection of materials by cranes or mechanical means.
Development of Heavy Equipment Movement Safety System covers :
- Manual Hoisting systems
- Electrical and Air powered overhead hoists and cranes
- Overhead Hoisting Monorails and Lifting Lugs
- Inspection and maintenance
- Operation
The GHS is an acronym for The Globally Harmonized System of Classification and Labeling of Chemicals. The GHS is a system for standardizing and harmonizing the classification and labeling of chemicals. It is a logical and comprehensive approach to:
- Defining health, physical and environmental hazards of chemicals;
- Creating classification processes that use available data on chemicals for comparison with the defined hazard criteria;
- Communicating hazard information, as well as protective measures, on labels and Safety Data Sheets (SDS).
The GHS itself is not a regulation or a standard.
Machines do not run themselves, they require operators and for the operator to work at his most efficient the machine, the type of safeguard and layout of controls and instrumentation must be such that they assist rather than hinder the operator.
- The behavior of the operators, service engineers and others involved, also has an influence on the safe use of machinery.
- The environmental conditions under which machines have to be operated is another factor in the complex formula of influences on safety in machine operations ( physical layout, provision of services, access, lighting, noise etc.)
Increasingly today the engineer, whether designer, producer or maintenance, is faced with more and more complex machinery in a society that is demanding higher and higher levels of protection for its members who have to operate machines. As a result there has been a proliferation of laws, standards and practices aimed at ensuring that an adequate level of protection is provided.
The Machine guarding adequacy covers principles involved in the protection techniques, the methods of application of safety equipment, sufficient basic information to enable a rational and reasonable selection, Economically viable and ensure that the degree of protection demanded by laws and society is achieved.
The guarding techniques required to protect against a single simple hazard and develops to encompass complex guarding problems associated with modern technically complex machines. For the more complex and technically advanced protection systems specialist advice may be required that can only be provided by the manufacturers of the protective equipment concerned.
The design of mechanical guards has changed little in recent years although its base may have been widened by the introduction of new materials and manufacturing techniques. However, the area in which the greatest changes have occurred is in the use of electronic and programmable electronic control and safety circuits. This is a rapidly developing field, advancing in parallel with developments in computer and software technologies and is spawning a growing number of standards.
Machinery Risk Assessment covers :
1. Safe Guarding Strategy :
- Design Considerations
- Factors affecting the Selection and Effectiveness of machine safeguards
- Typical Hazards of Machinery
- Risk Assessment, Risk Reduction and Selection of safeguards
2. Guarding Techniques :
- Mechanical Guarding
- Interlocking Safeguards
- Ergonomic aspects of machinery safeguarding
3. Safeguarding Systems :
- Mechanical safety arrangements
- Electrical safety circuits
- Hydraulic safety circuits
- Pneumatic safety circuits
4. Other Safety related arrangements :
- Safety in the use of Lifting equipment
- Safety with Pressure systems
- Safe working with equipment
- Plant Layout and Work Environment
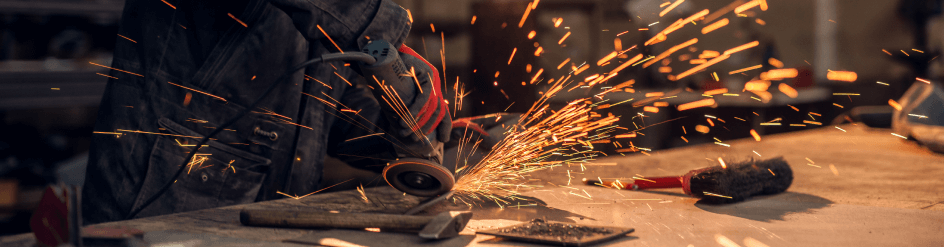
Need help? Call us Today +91 7600 60 48 20
Register your query and our response team will address your concern. Contact us